Melden Sie sich für unseren monatlichen Newsletter an,
und bleiben Sie zu HFLOR/HIMACS-Designtrends und Neuheiten auf dem Laufenden.
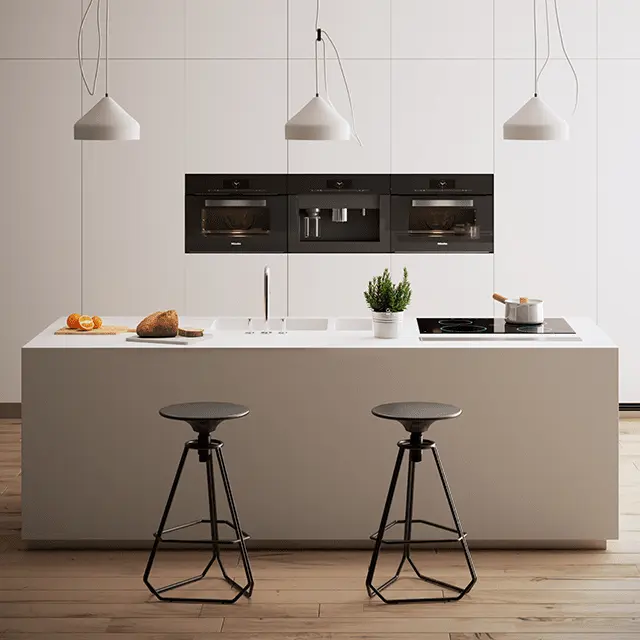
HIMACS: SLO_GEN table
Besucher bei Gensler staunen über mit HIMACS hergestellten organischen SLO_GEN Tisch
In der Lobby des Architekturbüros Gensler in Los Angeles steht der Gemeinschaftstisch SLO_Gen seit kurzem im Mittelpunkt des Interesses. Entstanden ist er in einer innovativen Partnerschaft zwischen Gensler und der Architekturfakultät am College of Architecture and Environmental Design der Cal Poly in San Luis Obispo (Kalifornien).
Aufgrund der für HIMACS typischen Eigenschaften, z.B. thermoplastische Verformbarkeit, Beständigkeit, fugenlose Verarbeitung und eine glatte Oberfläche, waren Architekten und Ingenieure von Anbeginn überzeugt, mit diesem Material die angestrebten verblüffenden und außergewöhnlichen Krümmungen erzielen zu können.
2011 kontaktierten Professoren. Jim Doerfler und Mark Cabrinha Ko-Direktoren des Cal Poly`s Digital Fabrication Lab (“d[Fab]Lab”) den Designchef Shawn Gehle Gensler L.A., um einen komplett virtuellen Entwurf mit Schwerpunkt auf digitaler Herstellung und unter Verwendung einer Online- Kollaboration zu schaffen .
Gehle reagierte und entwickelte ein einzigartiges zehnwöchiges Seminar, das den Studenten Zugang zur Design-Kompetenz des Unternehmens verschaffte und ihnen die Möglichkeit bot, durch die Gestaltung eines maßgeschneiderten Möbelstücks Formfindungstechniken und digitale Fertigungsprozesse zu erlernen.
Die Gestaltungsvorgaben skizzierten einfach ein Objekt, das Steh- und Sitzplatz für Gäste bieten konnte und in dem die Designpublikationen der Firma untergebracht werden konnten. Es sollte spezifisch auf den Einsatzort abgestimmt werden und im neuen Gensler Büro in der City von Los Angeles an prominenter Stelle Platz finden.
Ein virtueller 3D-Prototyp
Nach einer ersten persönlichen Kontaktaufnahme trafen sich die Cal-Poly-Studenten und die Fakultätsmitglieder des d[Fab]Lab mit Beratern von Gensler über das Online-Tool GoToMeeting, um im Zuge der Zusammenarbeit wöchentliche Seminardiskussionen durchzuführen und die erzielten Fortschritte des Teams zu überprüfen. Mit dieser Methode konnten die 300 Meilen Entfernung zwischen den Designern in Los Angeles und den Studenten und der Fakultät in San Luis Obispo überbrückt werden. Die professionellen Berater und Materialexperten konnten problemlos am Prozess teilnehmen, und die Studenten wurden mit einer Art der virtuellen Kollaboration konfrontiert, wie sie heute in der professionellen Praxis üblich ist. Im Blickpunkt blieb dabei stets der digitale Workflow – auch der Design- und Dokumentationsprozess des Teams wurde virtuell durchgeführt, die herkömmlichen 2D-Zeichnungen wurden durch ein 3D-Modell als Projektleistung für die Produktion ersetzt.
Im Verlauf des Seminars wurden die ursprünglichen Konzepte von drei Studenten mithilfe der 3D- Software Rhino und T-Splines weiterentwickelt und verfeinert; sowie virtuell überprüft und wöchentlich mit den Design-Team von Gensler kritisch besprochen.
Die Ingenieure des Buro Happold und LX Hausys als Lieferant des Solid-Surface-Materials HIMACS nahmen an zahlreichen Besprechungen teil, begutachteten die Pläne und lieferten Hinweise zur Durchführbarkeit der Konstruktion, den Kosten und der strukturellen Integrität. Bei einem letzten persönlichen Meeting in Los Angeles konzentrierten sich die Teilnehmer auf die Prüfung der physikalischen Eigenschaften und der Materialproben. Das Team was so in der Lage zu beurteilen, ob ein Glasfasermaterial oder das Solid-Surface-Material HIMACS die Herausforderungen des für den Tisch als vorherrschendes Oberflächenmaterial geplanten Werkstoffs erfüllen konnte.
Design und Einsatzmöglichkeit erschienen LX Hausys so attraktiv, dass das Unternehmen schließlich als Partner in das Projekt einstieg und das technische Know-how über das firmeneigene Solid-Surface-Material HIMACS einbrachte, das sich als idealer Werkstoff erwies, um den Drapiereffekt der Tischoberfläche zu erzielen. Zur Unterstützung durch LX Hausys gehörte auch die Herstellung des Kontakts zum Fertigungsspezialisten R.D. Wing Co. Inc. in Seattle, der letztendlich für die Konstruktion und Lieferung des Tisches sorgte.
Der SLO-GEN Tisch würde kürzlich in der Hauptlobby von Gensler in Los Angeles aufgebaut. Seither ist er dank seiner dramatischen Konturen ein Blickfang für vorbeigehende Passanten und immer wieder Anlass für Fragen nach seiner Entstehungsgeschichte. HIMACS lässt sich hervorragend mit anderen Materialien kombinieren. Die weiß gehaltene Oberfläche und der
natürliche Holzton bilden einen subtilen und eleganten Kontrast.
Die Integration von Sperrholz und HIMACS Solid Surface
Die Schneidepfade für die Sperrholzrippen des Tischs wurden aus dem 3D-Modell entnommen und für die CNC- Bearbeitung auf 1,2 x 2,4 m großen Europly-Platten ausgelegt. Um alle Rippenelemente für den Tisch auszuschneiden, waren zwölf Sperrholzplatten nötig. Während des Bearbeitungsverfahrens wurden entlang der Rippenkanten Laschen stehen gelassen, um die Rippen miteinander zu verbinden und den Abnahmeverlauf zu stabilisieren. Diese Laschen wurden letztendlich beschnitten, abgefeilt und von Hand geschmirgelt. Der Sinn dieser Herstellungsmethode war es, die Formen während der maschinellen Bearbeitung festzuhalten und Klappern zu verhindern sowie Beschädigungen der Sichtflächen durch Klebeband oder Schrauben auszuschließen. Nach dem Entfernen der Laschen wurden die Rippen matt lackiert. Nach dem Trocknen des Lacks, wurde der „Eierkarton“ mit Hilfe eines Gummihammers und Quernuten von Hand montiert.
Die thermische Verformung von HIMACS und die Kombination mit Holz
Zunächst wurde die S-förmige Deckplatte auf einer CNC-Fräsanlage in vier separaten Teilen aus HIMACS gefräst. Die Anzahl der Stücke ergab sich aus der begrenzten Größe des Ausgangsmaterials und der Gesamtgröße der Tischhülle. Die so entstandenen einzelnen Stücke wurden dann zusammengeklebt und glatt
geschmirgelt - sie stellen den einzigen "flachen" Teil der Tischoberfläche dar.
Dann wurde maschinell ein 1,5 m breiter Streifen (in mehreren T eilen) hergestellt, der der geschwungenen Linie der Tischoberfläche folgt. Dieser Streifen wurde an der Stelle als Sicherungsband eingesetzt, an der die Seitenwand des Tischs auf die Unterseite der Abdeckplatte trifft. Der Streifen wurde festgeklebt, wobei in das Profil wellenförmige Unebenheiten eingearbeitet wurde, die es der Werkstatt später im weiteren Verfahren erleichtern sollten, die Seitenwände auszurichten.
Angesichts der starken Krümmung in den aus HIMACS gefertigten Seitenverkleidungen des Tischs war die Entscheidung schwierig, wie die Paneele eingeteilt und geformt werden sollten. In diesem Fertigungsschritt musste entschieden werden, welche T eile der Solid-Surface- Oberfläche ohne Formwerkzeuge maschinell geformt werden konnten, welche Teile Formen benötigten und was für Formen dies sein mussten, und wo und wie man die Tischhülle am besten in Paneele aufteilen konnte, um das von LX Hausys gelieferte Material optimal zu nutzen.
Um einen optimalen Materialeinsatz zu erzielen
und die Verarbeitung der Solid-Surface-Flächen zu verbessern, wurden alle Seiten des Tisches in fünf Teilstücke unterteilt, basierend auf der Topographie der jeweiligen individuellen Oberfläche. R.D. Wing baute für die Herstellung jeder Seitenwand unterschiedliche Formen, wobei keine Form mit einer anderen identisch ist. Um die kompliziertesten Teile der Seitenwand in den Griff zu bekommen, gab es nur eine Möglichkeit: den Einsatz einer Klappform (sog. Clamshell Mould). Bei dieser Technik müssen für jedes zu formende Teilstück zwei Formen gefräst werden – eine männliche und eine weibliche So kann gleichzeitig von vorn und von hinten Druck ausgeübt und damit das Solid-Surface-Material thermisch geformt werden.
Für die Fertigung der Formen verwendete R.D. Wing recycelten 15/20-pound Polyurethanschaum. Die Seiten der Schaumstoff-Formen blieben unbearbeitet, weil dadurch die Formen für jedes Teilstück bis zu zehn Mal benutzt werden konnten. Der Schaumstoff wurde auf einen MDF-Sockel montiert und mit einer CNC-Fräsanlage in Stapel von 1,27 cm gefräst. Jede Schicht wurde maschinell bearbeitet, danach wurde darauf eine neue Schicht Material aufgebracht. Dieser Vorgang wurde so lange wiederholt, bis eine komplette Form hergestellt war. Bei der Bearbeitung wurde auf eine knappe seitliche Zustellung geachtet, um ohne Schmirgeln auszukommen. Am Perimeter der Formen wurde eine Trimmlinie angebracht, damit die Werkstatt sehen konnte, wie ein Paneel an das andere passt. Nach der Fertigstellung aller Formen und der Entfernung des überschüssigen Schaums wurde zur Wärmeableitung eine Baumwollschicht auf die Oberfläche aufgebracht.
Die größten Teile aus HIMACS, die eine thermische Verformung in zwei Richtungen erforderten (komplexe Krümmungen), wurden erwärmt. Nach der Erwärmung wurden sie in die Klappform gelegt. Für die Herstellung aller Seitenteile in den fünf Formen benötigte man zwölf einzelne HIMACS Teile. Wie viele Einzelteile gebraucht wurden, wurde nach der Trial-and-Error-Methode entschieden. Als die zwölf Teile in ihrer Rohform fertig waren, kamen sie zurück in die Form und wurden schließlich für den endgültigen Zuschnitt ausgelegt. Jedes Teil wurde an das entsprechende Anschlussstück angepasst und mit Hilfe der Form verklebt. Die kleineren Teile wurden verschweißt, bis fünf Hauptelemente hergestellt waren.
Die Seitenteile wurden zu fünf brauchbaren Stücken vorgeklebt und dann auf die Seiten der Holzstruktur aufgebracht. Die Seitenteile wurden an die Unterseite des Tischs gegen den Randstreifen unter Einbeziehung der Abdeckung angepasst, wobei die Seiten fest an die Holzstruktur gepresst wurden und die gesamte Konstruktion vor dem Schweißen zusammengezogen wurde.
Als nächstes wurde die Unterseite und die Seite zu den Regalen hin bündig zurecht geschnittenen, danach die verschweißte Seite gerade geschnitten und eine flache Kante geschaffen, die an die Unterseite es Tisches anstoßen sollte. Nachdem das erste Teilstück an der Unterseite des Tischs befestigt und die Rückseite des ersten Teilstücks mit Silikon an der Holzstruktur angebracht war, wurde das zweite Teilstück vorläufig an die Unterseite des Tischs und das entsprechende Teilstück angepasst. Dieser Ansatz setzte voraus, dass die Form mit so wenig Spiel wie möglich zugeschnitten und zur endgültigen Anpassung von Hand zurecht gefeilt wurde. Sobald das Teilstück genau passte, wurde der Vorgang entlang des Perimeters wiederholt.
Nach dem Verkleben aller Teilstücke, wurden alle exponierten Oberflächen geschmirgelt. In der abschließenden Phase wurde die gesamte Oberfläche erneut geschliffen und kleinere Mängel beseitigt.
Nach dem Zusammenbau wurde der komplette Tisch für den Versand und die Auslieferung in eine eigens dafür angefertigte Kiste gepackt.
Standort | Gensler Los Angeles, Los Angeles (California, USA) |
Architecture & Design | Cal Poly, San Luis Obispo, Department of Architecture, College of Architecture and Environmental Design Faculty: Jim Doerfler, Mark Cabrinha Students: Ben Hait-Campbell, Cory Walker, Kegan Charles Flanderka Gensler LA |
Fabrikation | R.D. Wing Co., Inc. |
Bildnachweis | ©Gensler Los Angeles |
Pressemitteilung Pressemitteilung herunterladen |
Projektgallerie
-
Bilder herunterladen
Wenn Sie ein Journalist sind, können Sie die gewünschten Medien auswählen und uns bitten, sie in HD zu liefern.
PROJEKTFOTOS BESTELLEN -
Bilder herunterladen
Wenn Sie ein Journalist sind, können Sie die gewünschten Medien auswählen und uns bitten, sie in HD zu liefern.
PROJEKTFOTOS BESTELLEN -
Bilder herunterladen
Wenn Sie ein Journalist sind, können Sie die gewünschten Medien auswählen und uns bitten, sie in HD zu liefern.
PROJEKTFOTOS BESTELLEN -
Bilder herunterladen
Wenn Sie ein Journalist sind, können Sie die gewünschten Medien auswählen und uns bitten, sie in HD zu liefern.
PROJEKTFOTOS BESTELLEN -
Bilder herunterladen
Wenn Sie ein Journalist sind, können Sie die gewünschten Medien auswählen und uns bitten, sie in HD zu liefern.
PROJEKTFOTOS BESTELLEN -
Bilder herunterladen
Wenn Sie ein Journalist sind, können Sie die gewünschten Medien auswählen und uns bitten, sie in HD zu liefern.
PROJEKTFOTOS BESTELLEN -
Bilder herunterladen
Wenn Sie ein Journalist sind, können Sie die gewünschten Medien auswählen und uns bitten, sie in HD zu liefern.
PROJEKTFOTOS BESTELLEN -
Bilder herunterladen
Wenn Sie ein Journalist sind, können Sie die gewünschten Medien auswählen und uns bitten, sie in HD zu liefern.
PROJEKTFOTOS BESTELLEN -
Bilder herunterladen
Wenn Sie ein Journalist sind, können Sie die gewünschten Medien auswählen und uns bitten, sie in HD zu liefern.
PROJEKTFOTOS BESTELLEN -
Bilder herunterladen
Wenn Sie ein Journalist sind, können Sie die gewünschten Medien auswählen und uns bitten, sie in HD zu liefern.
PROJEKTFOTOS BESTELLEN -
Bilder herunterladen
Wenn Sie ein Journalist sind, können Sie die gewünschten Medien auswählen und uns bitten, sie in HD zu liefern.
PROJEKTFOTOS BESTELLEN
Bildbibliothek

Zu Ihrem Bildarchiv hinzugefügt
Gehen Sie zur Seite Bildbibliothek, um HD-Bilder anzufordern, oder klicken Sie auf OK, um mit Ihrer Bildauswahl fortzufahren.
Medienkontakt
Mariana Fredes +41 (0) 79 693 46 99 mfredes@lxhausys.com
Agnieszka Papież +48 504 976 688 apapiez@lxhausys.com